Hello everyone and thanks for all the helpful comments.
I have cut a 115t 0.75m wheel as a test in 1/8″ cz120 and also a 115t 0.5 m wheel and both have turned out fine this time! at least as far as I can see. This time I have potographed the setup and scanned the wheels.
Before cutting I checked everything over very carefull, everything was tight and all slides locked and cut adjacent teeth until a tiny witness was left at the tip. They were then all cut at one pass as I normally do with the cutter running at about 4000rpm, the 0.75m blank should have been better supported but I coulnt find any suitable washers.
So it looks like the division plate was ok. I know it shouldnt make any difference but I I wondered about my blanks size calculation as the calculator batteries were almost flat, changed them but got the same numbers. My digital calipers are slightly magnetic and attrract swarf and you sometimes get a false zero.
I think that may have influnced my initial blanks size as the thin tooth wheels were 3.472″ dia and the one just cut is 3.484″ very close to the calculated 3.481″
So not really sure what went wrong but will recut them again when the replacement brass arrives, fingers crossed!
Regards Peter
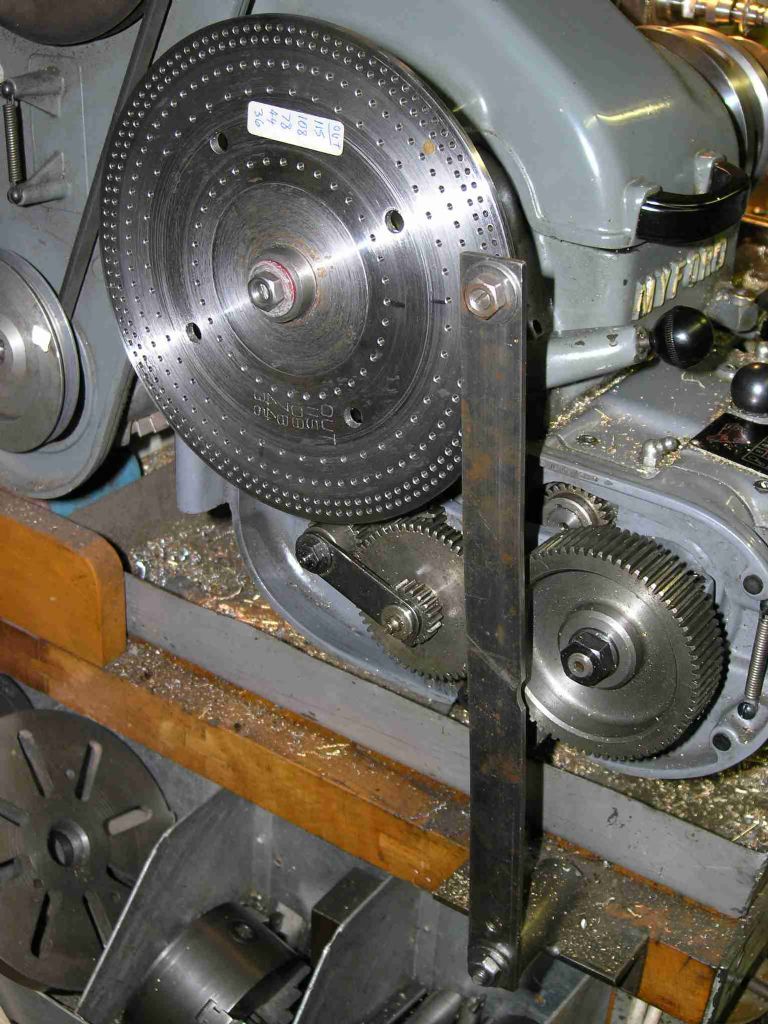