The following is the speeds I posted 10/25/2019 running the APC 8×6 propeller after machining the faces. The maximum speeds for 10, 15, 20, and 24 psig were 1,000, 1,125, 1,215, and 1,450 rpm respectively. After switching to the floating O-ring, the maximum speeds for 10, 15, 20, and 24 psig were 1,000, 1,250, 1,400 and 1,500 rpm respectively. I was able to maintain a pressure of 24 psig after machining the faces, 20 psig was the maximum I could maintain before machining the faces. After testing I took the cylinder off and tried moving the piston with the ports open and closed. The force to move the piston was very large with the port closed when moving toward the top cylinder cover. The force was quite a bit less with the port closed and moving toward the bottom of the cylinder due to leakage around the connecting rod. There was very little force required to move the piston in either direction with the ports open. Even with the much tighter clearance on the cylinder support shaft, the cylinder is pried away from the standard if the pressure is above 15 psig (1 bar). This only happens with the tight packing or floating O-ring. Tightening the spring to the maximum doesn’t keep the cylinder from being pried away. I believe the biggest weakness of the simple oscillating cylinder engines is the cylinder pin riding in a hole on one side only. If the seal is good on the piston, the force cocking the cylinder can be very large. If you make the spring large enough to keep the face of the cylinder from being pried away from the face of the standard, the friction loss becomes too large. From my testing with a relatively tight clearance on the cylinder pin, the best power came with the spring compressed less than the maximum. The flow lost by the cylinder cocking was still relatively low because of the tight clearance. The cylinder would tilt away from the standard each time the pressure was above 15 psig. This caused a leakage at higher pressures that limited the power. My airbrush compressor had to run continuously at pressures above 15 psig but could maintain pressures below 15 psig by running intermittently. Apparently, the friction and binding caused by the increased pressure partially offsets the gain in performance from having less leakage by the piston.
The following chart has been updated to show the tests with the floating O-ring and shows the maximum performance was about the same for the floating O-ring and bedded in packing.
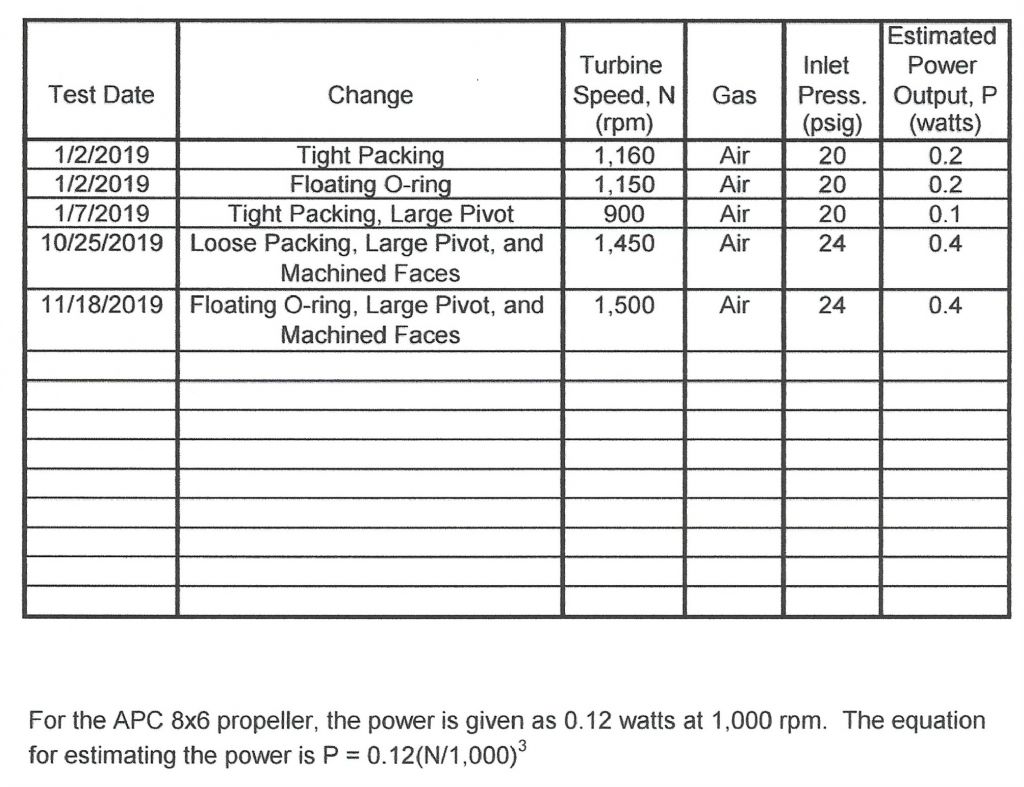