Depends on how early! The early builders had to sort out a lot of problems and develop new materials and methods as they went.
Early boilers were low pressure, and they leaked! Cow-dung is often mentioned as a gasket sealant, mixed with horse hair, with leather or paper padding etc. This sort of gasket may not last long, but they're cheap and easy to replace even in primitive circumstances.
Blowing down uses the pressure of the boiler itself to remove gunk, not necessarily doing a good job, and of course wasting a lot of coal. Had to be done very frequently at sea because marine boilers ran on salt water. The boiling point of salt water rises as it gets more salty, to the point the fire damages the boiler plates. Marine boilers had to be blown down much more often than land-based boilers.
At first no-one paid much attention to water purity, and this persisted on mainline rail because it was cheaper to fix boilers than to treat water. Pretty crude compared with marine steam, where water quality and treatments got attention. Running a marine engine for few months at sea with no easy access to fresh-water, coupled with a pressing need for fuel economy and high reliability meant better technology was introduced earlier. A locomotive breaking down between Paddington and Swindon is a tiny dirt cheap problem compared with a steamship breaking down between Perth and Suez. So ships usually had high-pressure pumps, condensers, water treatment, multi-stage and superheat before the railways. Easier to do on a ship because they have the space, even for a well-equipped workshop.
On land, the need for high-pressure steam soon asserted itself, and this led to the demise of cow-dung, in favour of factory made seals, and the need for clean water, and furnaces designed to burn cheap coal. High-pressure led to huge numbers of boiler explosions, so these too went up-market.
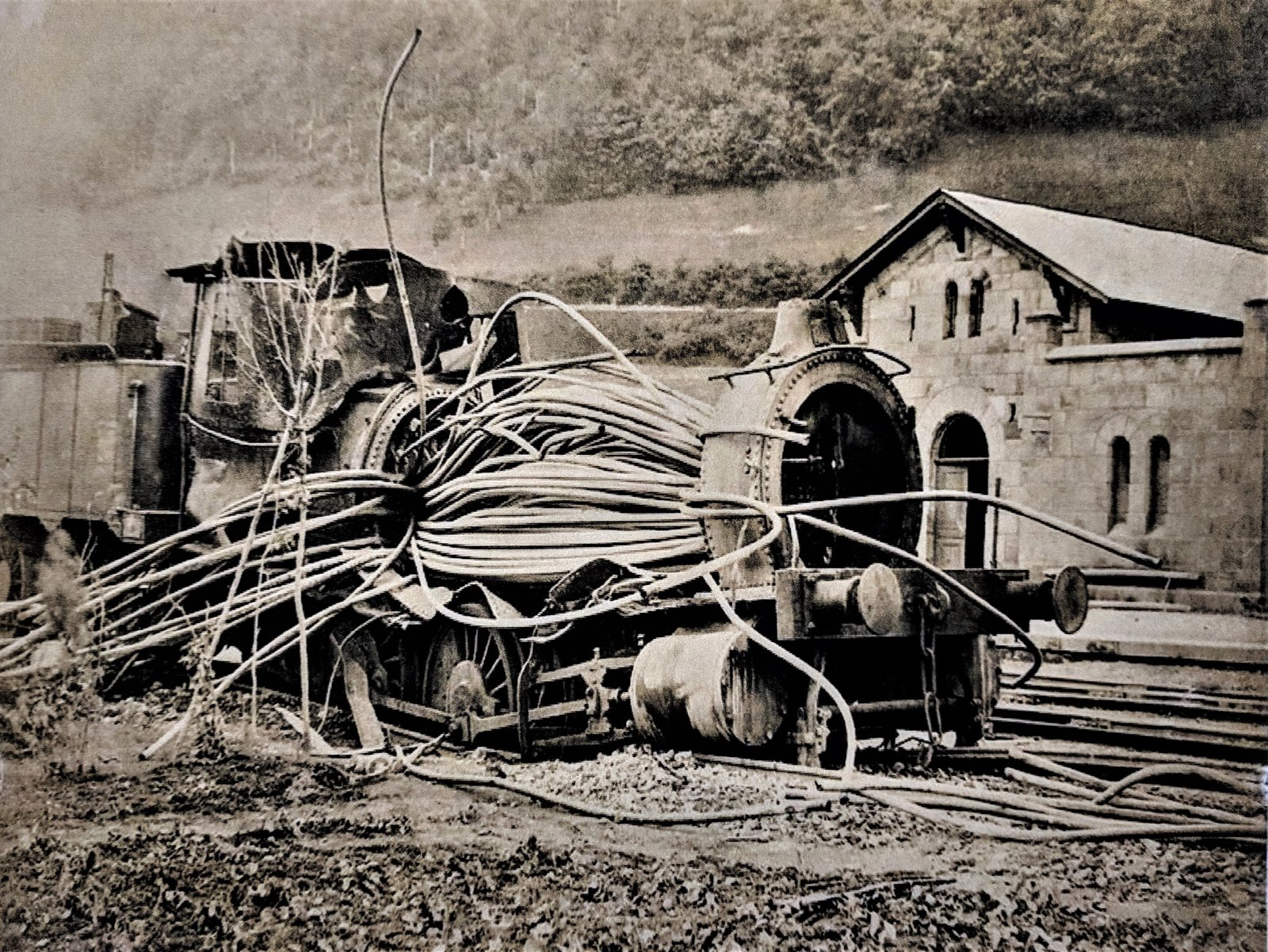
Road and rail locomotives remained something of a special case, because weight and size limitations restricted what could be done. Boiler inspections relied on men poking burning paraffin rags and mirrors through mud-holes well into the 20th century.
Not sure when high-pressure water was first used to clean boilers on the railways. Maybe early, though it's not mentioned in any of my books. An ordinary water tower requires something like a 25psi feed, and steam force pumps existed long before railway locomotives. Whether they were used or not on locomotives I don't know. My impression is they may have relied on a mix of high-pressure blow downs and/or rinsing out at ordinary water pressures.
The story is complicated by wide variations between different railways. Some were forward looking, properly equipped, and well-run, whilst others were sloppy in the extreme. The Wikipedia account of the 1876 accident near Radstock speaks volumes about the dreadful state of the Somerset and Dorset Railway at the time!
Dave