I avoid machining Stainless because most of them work-harden. By no means impossible, but expect trouble. Here's what the British Stainless Steel Association say, my bold:
When machining stainless steels it important to ensure that there is no dwell or rubbing caused by machine vibration or tool chatter. Machines must be ‘substantial’ and capable of making the deep cuts needed in machining austenitic stainless steel without slowing down the set feed or surface speeds. Small training or ‘hobbies’ lathes and milling machines intended for machining mild steel, brasses etc. are unlikely to be substantial enough for the successful machining of stainless steels.
By 'successful machining' they mean reliably cutting metal to size and finish commercially without needing a skilled operator to experiment for best results. All will be well using a rigid powerful machine fitted with the right type of cutter, spinning at the correct RPM, with a suitable Depth-of-Cut and steady Feed Rate, suitable lubrication/cooling, and a way keeping swarf out of the cutting area.
Of 316 Alco say:
316 stainless steel has good machinability. Machining can be enhanced using the following rules:
- ‹ Cutting edges must be kept sharp. Dull edges cause excess work hardening.
- ‹ Cuts should be light but deep enough to prevent work hardening by riding on the surface of the material.
- ‹ Chip breakers should be employed to assist in ensuring swarf remains clear of the work
- ‹ Low thermal conductivity of austenitic alloys results in heat concentrating at the cutting edges. This means coolants and lubricants are necessary and must be used in large quantities.
So the odds are stacked against small workshops. My WM18 does what I want, but it's not particularly rigid, or powerful, I only own a limited range of cutters, they're not all in good condition, my experience of stainless is limited, and I'm not a naturally talented machinist. Whilst I and the machine cut machinable alloys reliably well, I'm not surprised when any of the many difficult Alloys turns out to be a challenge. I avoid scrap unless I know what it is.
SD's photos show, I think, the result of work-hardening. Rather than cutting, the cutter is rubbing and bouncing along the surface. Rubbing hardens the surface so effectively that HSS struggles to penetrate and is rapidly blunted, the end.
All is not lost! The finish can be improved by using an inexpensive Belt Sander like this example as a Linisher:
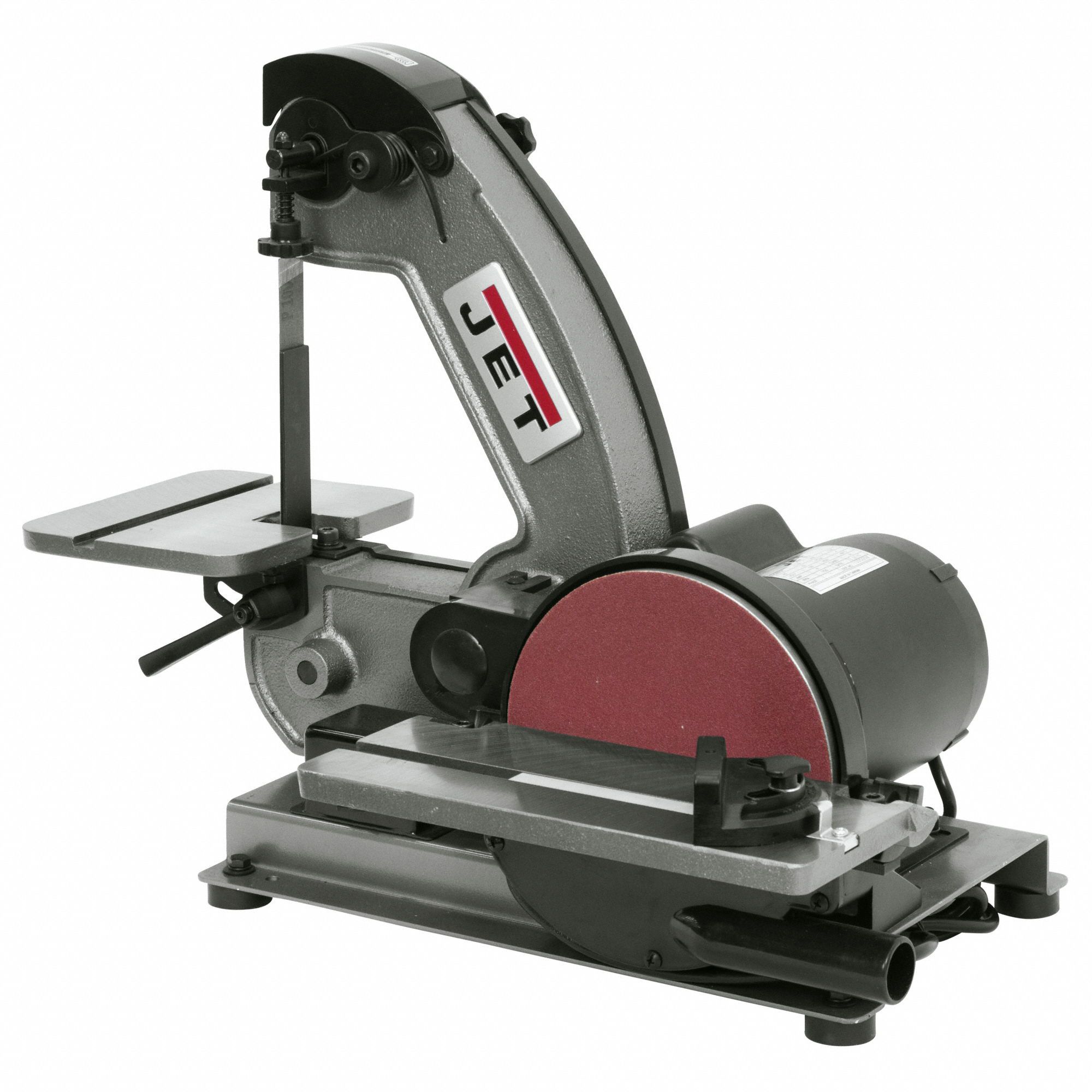
Not sure what others find, but in my workshop milling and lathe cut surfaces often benefit from a mild abrasive touch-up. Depends on the material, but ordinary mild-steel usually gets a licking because it's a bit smeary. Leaded mild-steel, 6082 Ali and Brass are more likely to come clean off the machine.
Dave