As mentioned in my introductory post a few weeks ago, I'm currently working on building an ME Boiler to power my recently completed Stuart 10V.
So I thought I'd post an update of the progress I've made since then.
I was in the process of making the components for the firebox and burner, which you can again see here.
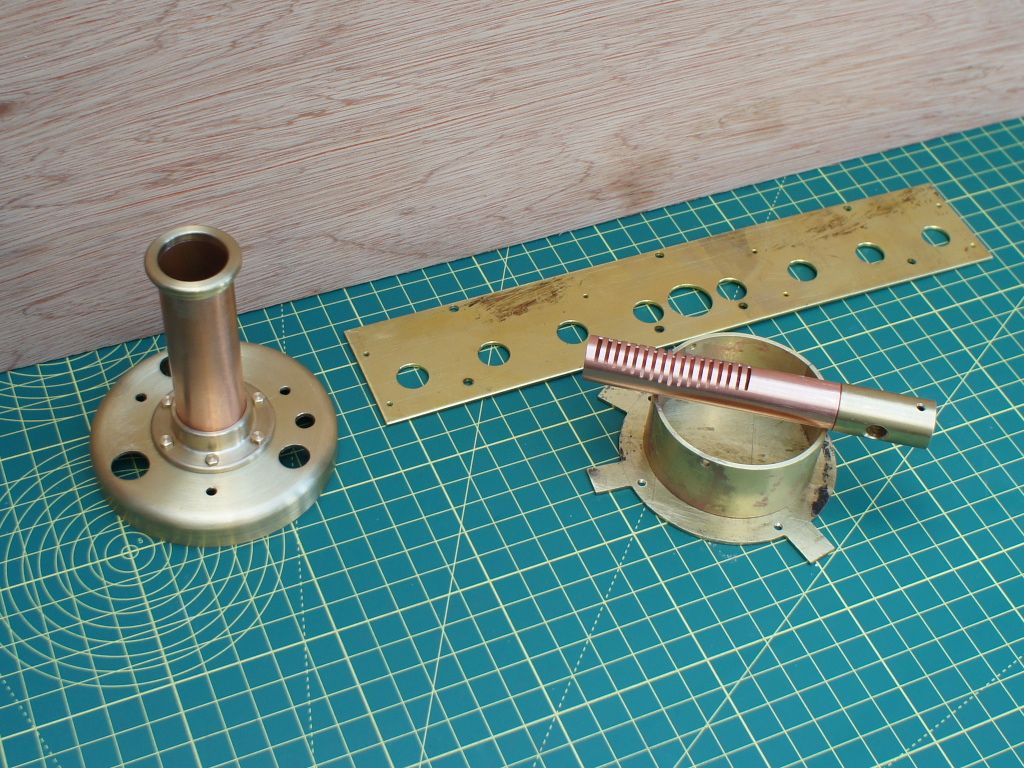
And I've now formed and silver soldered the firebox, along with the rest of the components for the burner which are test fitted together with a camping gas regulator and hose.
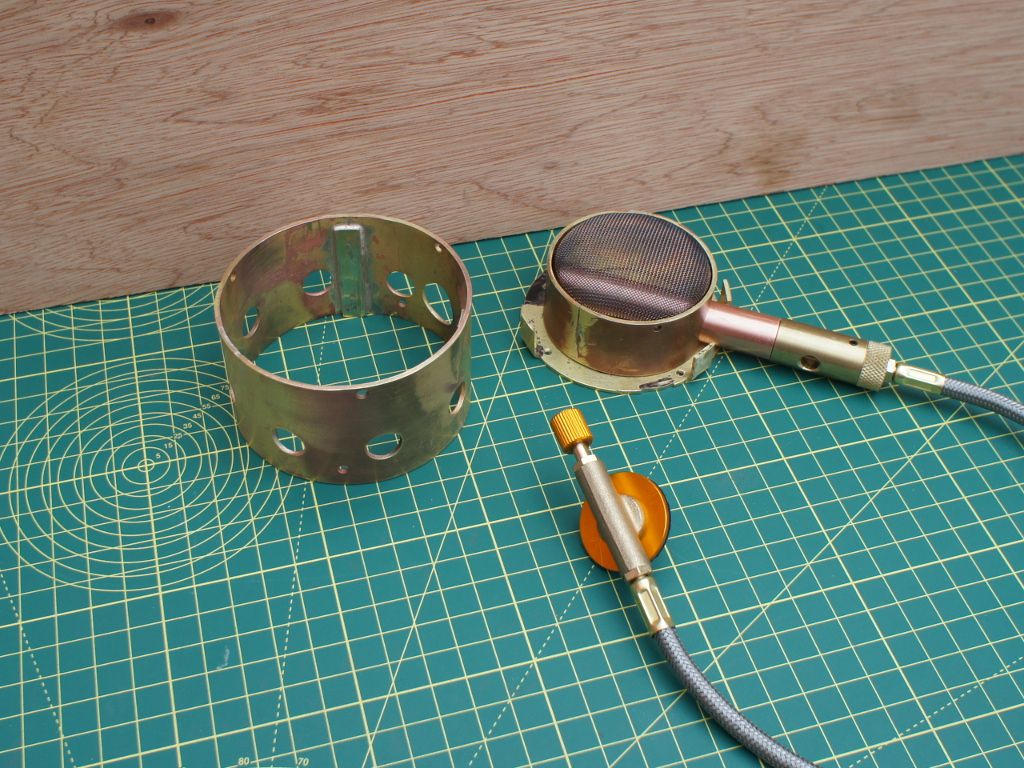
The burner components and firebox base silver soldered together
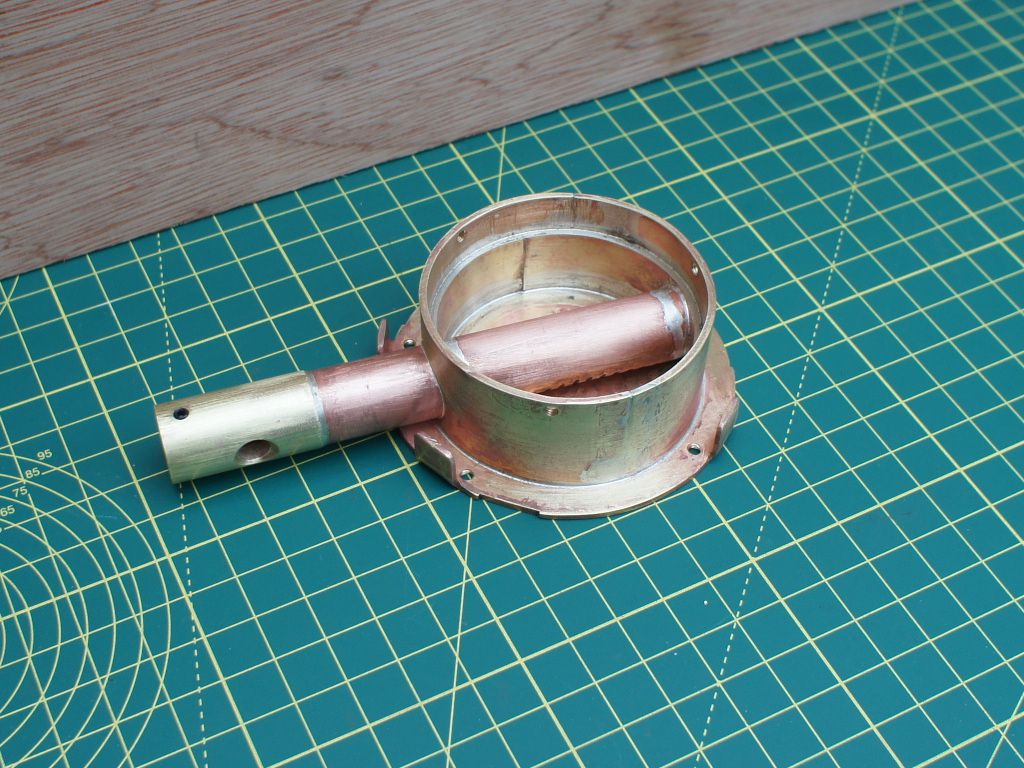
I also had a go at drilling my own gas jet.
The design calls for a No8 jet, which appears to be 0.25mm. The smallest drill I had was 0.3, so I went with that for now.
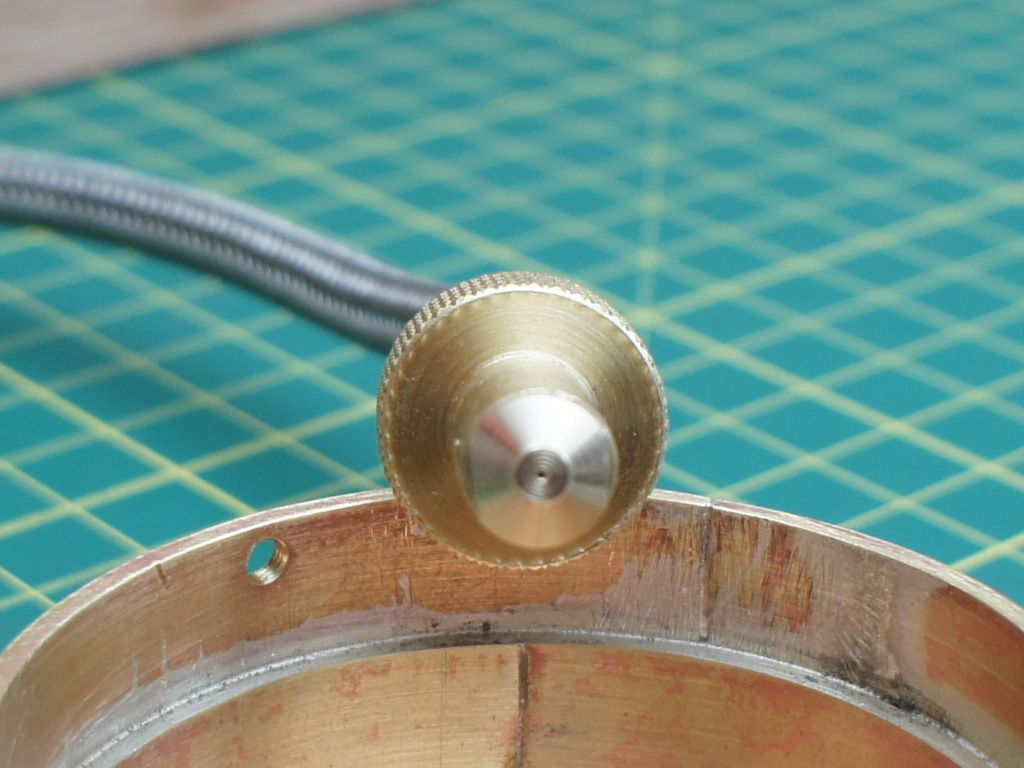
And, it works!
The flame is a bit large when the regulator is fully open, due to the slightly bigger jet size, but is otherwise stable and burns cleanly over the full range.
I can tweak it later once it's running in the firebox with the boiler fitted.

I also made up the various parts for the hand pump, which I had been putting off, as I thought having the rather blocky pump just sitting there on the base ruins the look somewhat.
In the end I decided to go with the pump roughly as designed, but make a few changes such as the side plates you can see here.

The reason for this is that I'm going to fit it inside a 'water tower', which you can see the basic setup of here alongside the other boiler parts.
