Nick your still not with me.
Traversing out doing internal threading needs a relief where by you can use it as a start point.
If cannot have a relief (thread just ends) you have to do conventionally should i say, straight in right to left. The only piccy i have not thread mentioned above just to show internal thread ends with no undercut at the end running in to a taper. No way can traverse out cannot feed the cutter in theres metal there and will break the cutter tip.
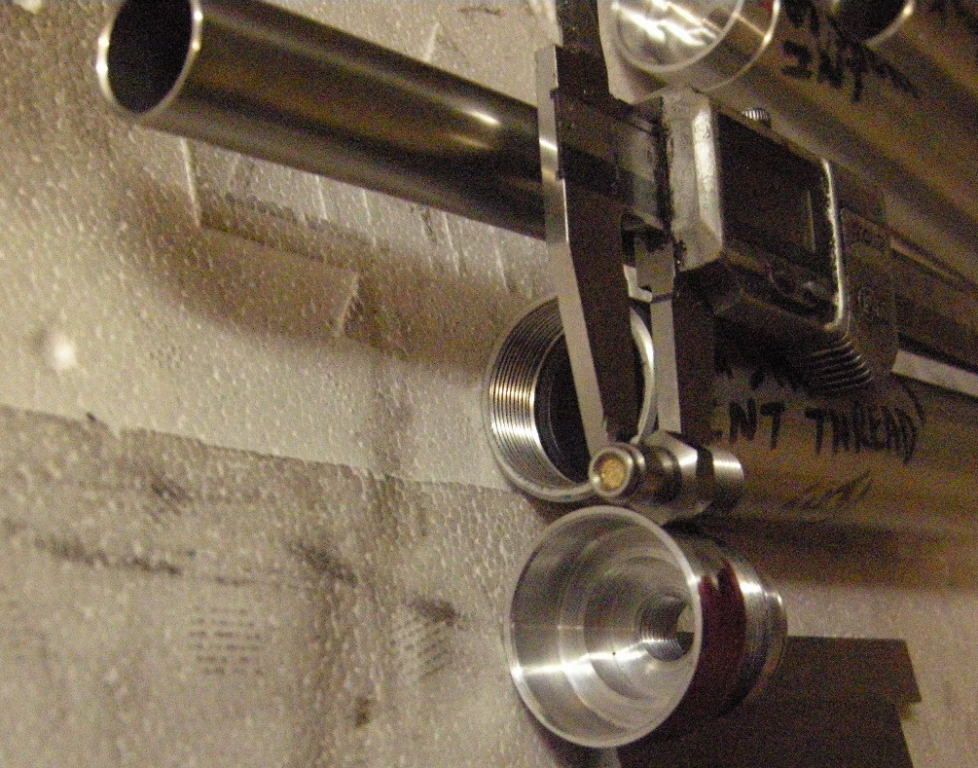
The other point even if there is a relief at back of the internal thread you still have to manually reposition to exact start point every pass revolving the chuck by hand over coming the torque (ok in mid ranges.) Jog function absolutely useless when might be 1/8 to 7/8 of a rev to line up, guarantee breaking a tip and or scrapping the job if up against a face at start point.
Those Iscar bars are unreal, one of my favourite and best tools ever bought with thru coolant, totally stunning in what they can do with ease. The tips are dear over £30 each shopping around for the larger 16mm shanked one with min bore size 18mm dia. Sometimes i will whip it out the holder and mill with it and change to 2.2mm rad, 45×45 degree or flat ended parting.
MGCH 06 min bore size is 9.6mm, you have discounted the tip protruding.
Nightmare like all tooling companies deciphering the tips to go with the tooling. Some of my Iscar for that type of tool are meant for a totally different tool, key is the 3 prongue front fixing and screw work off that.
Edited By Jon on 25/07/2018 11:55:26
Edited By Jon on 25/07/2018 11:57:14