I'm not familiar with the John Haining drawings. However, I have made a number of bevel gears for my traction engines.
There are two (approximate) methods of cutting bevel gears on a manual milling machine. Straight tooth bevel gears are normally designed using the pitch circle diameter and other parameters at the outer edge of the gear. From your description this is how the John Haining drawings are specified. To cut the bevel gears specified at the outer edge you use an involute cutter of the DP specified at the outer edge. The number of cutter is not directly related to the number of teeth on the gear, but that is not important in this discussion. A standard involute cutter will have the correct tooth curvature, but will be too wide to form the inner tooth shape. So special involute cutters were made for bevel gears. These are the ones in your box labelled "BEVEL". The tooth form will be for a 12DP gear but will be narrower than normal. These are used for the three cuts, the first cut forming the inner shape of the tooth at the correct width, and the second and third cuts widening the outer edge while not affecting the inner edge. This method does not give the correct curvature at the inner edge of the teeth – they will need to be filed, or run-in, to get a good fit. I've used this method once, some 40+ years ago. I think that "BEVEL" involute cutters are no longer commercially available.
The second approach is the parallel depth method, this is the one described in the Ivan Law book. In this method the gears are designed using the PCD and other parameters at the inner edge of the gear. This means that standard involute cutters can be used. Other than that the three cuts are as for the first method. As implied by the name the depth of the teeth is constant, not varying as in a true bevel gear, but the gears will run perfectly well. I've not used this method, although I have played with the maths when designing the bevel gears for my traction engines.
For my engines I ignored all the above and modelled the 6DP bevel gears in 3D CAD and machined them on a CNC mill, as I wanted to see if I could produce true bevel gears:
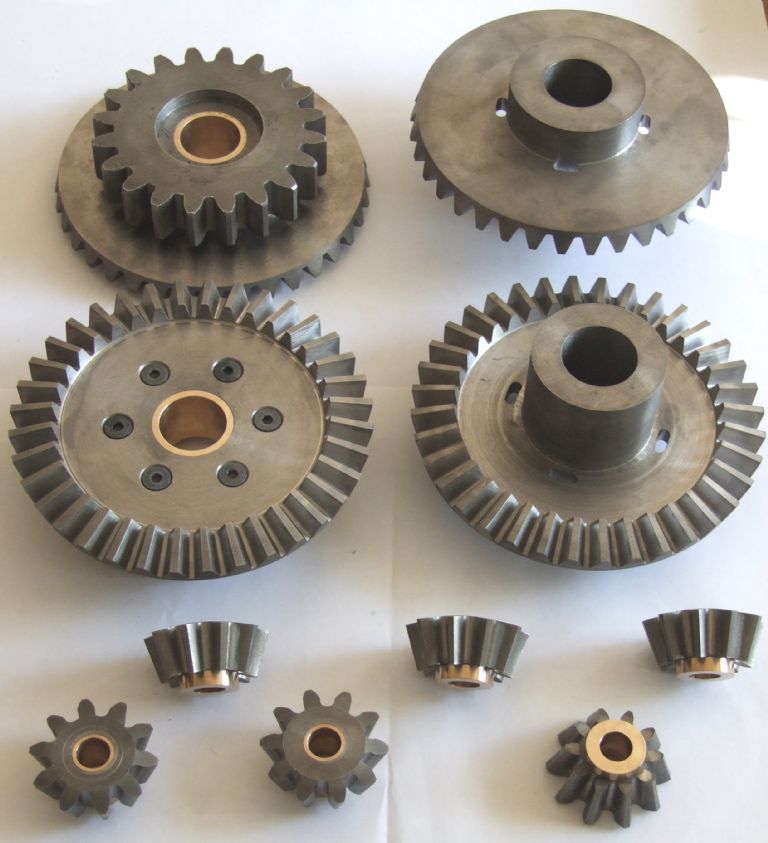
And the 16DP ones I made for the governors:

Andrew