Must be getting old, I thought I made my 6DP traction engine crankshaft gears from EN8, but looking back I actually made them from EN24T. Gears shown here, before the splines were machined:

If I recall correctly I had to turn at fairly high speeds to get the nice finish with insert tooling; probably 800 or 1200rpm. Depth of cut and feeds were nothing special.
I cut the gears in one pass; anything else is a waste of time and just increases wear on the cutter. Spindle speed would have been around 60rpm. I can't remember what the feedrate was, but I normally aim for around 4 thou per tooth when horizontal milling. Anything much less and the mill shakes. Gear cutting shown here; coolant not essential but it does help cool things down:
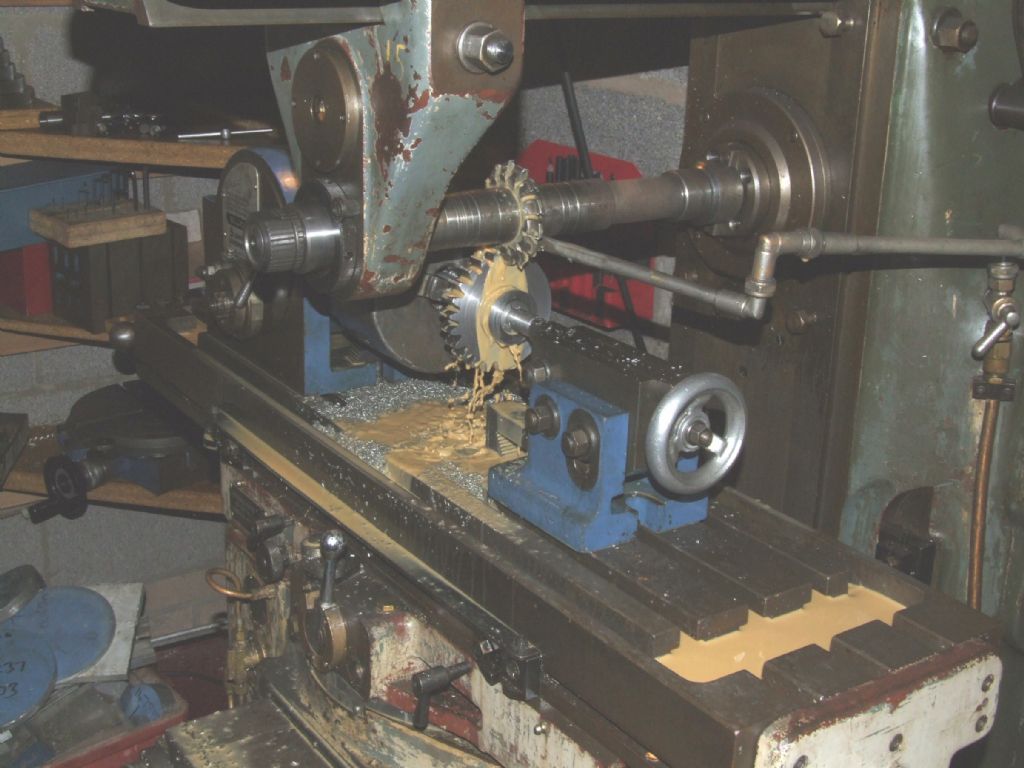
The cutter was secondhand, bought from the US via Ebay. A new cutter should cut a complete gear without a problem, although it may depend upon the source of said cutter.
Andrew