One topic that crops up fairly regularly on the forum is clocking the fixed jaw of a vice true to the X-Axis with many finding it a lengthy process and then once they do eventually get the vice clocked true they are reluctant to remove it to make full use of the milling machine. One option to speed up this process so that you can get the most time actually using the mill is to fit keys to the base of the vice which locate against the edge of a tee slot and make fitting the vice quick and repeatable to within acceptable limits for most work.
For this example I will be using an 80mm versatile vice from ARC Eurotrade which comes complete with a swivelling base, universal keys and the slot already milled in the base of the vice and holes tapped to attach the keys. The swivel base is best removed and stored for the odd occasions when it may be needed which will give more head room and also save humping such a weight on and off the Mill’s table.
The first thing to do is check what width the upper narrow section of your tee slots are, a small mill is likely to be 10mm, a large one 14 or 16mm or in the case of the SIEG SX2.7 that I will be using 12mm. Older machines will have similar imperial width slots. Photo 1. Next check the width of the supplied keys in the case of this size of vice they are 14mm Photo 2 which conveniently gives us some material to come off allowing their fit into the tee slots to be fine tuned. Don’t worry if your keys are less than the width of your slots, they can still just have a small amount skimmed off them to bring them into line.
Enjoy more Model Engineer reading in the monthly magazine.
Click here to subscribe & save.
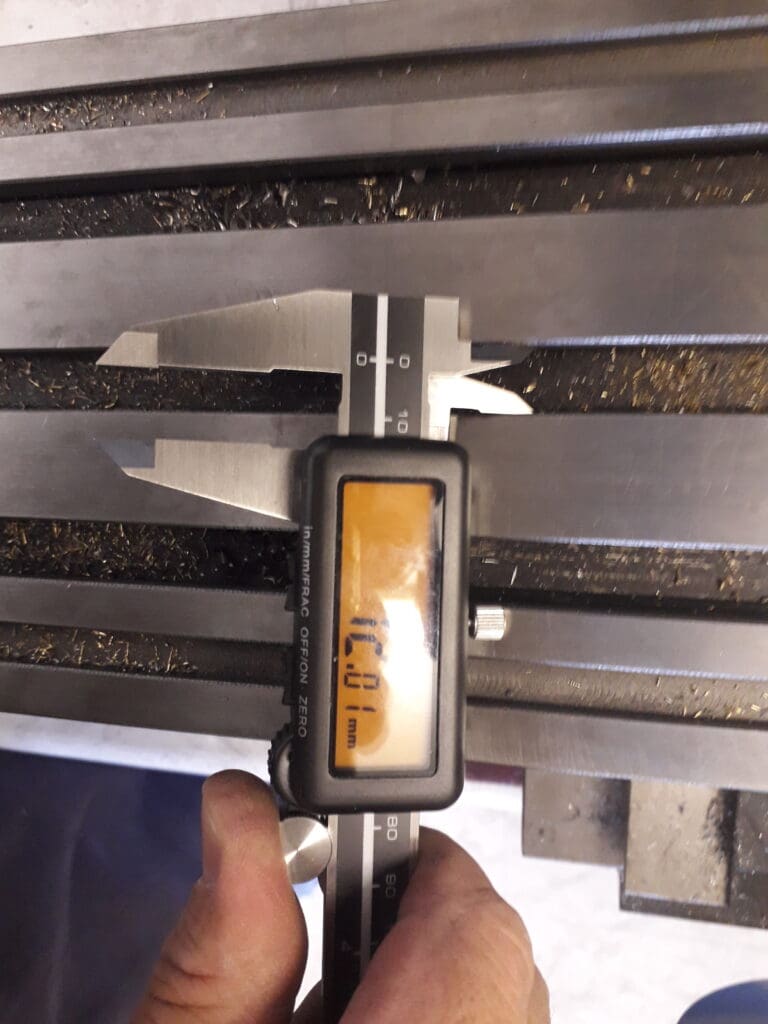
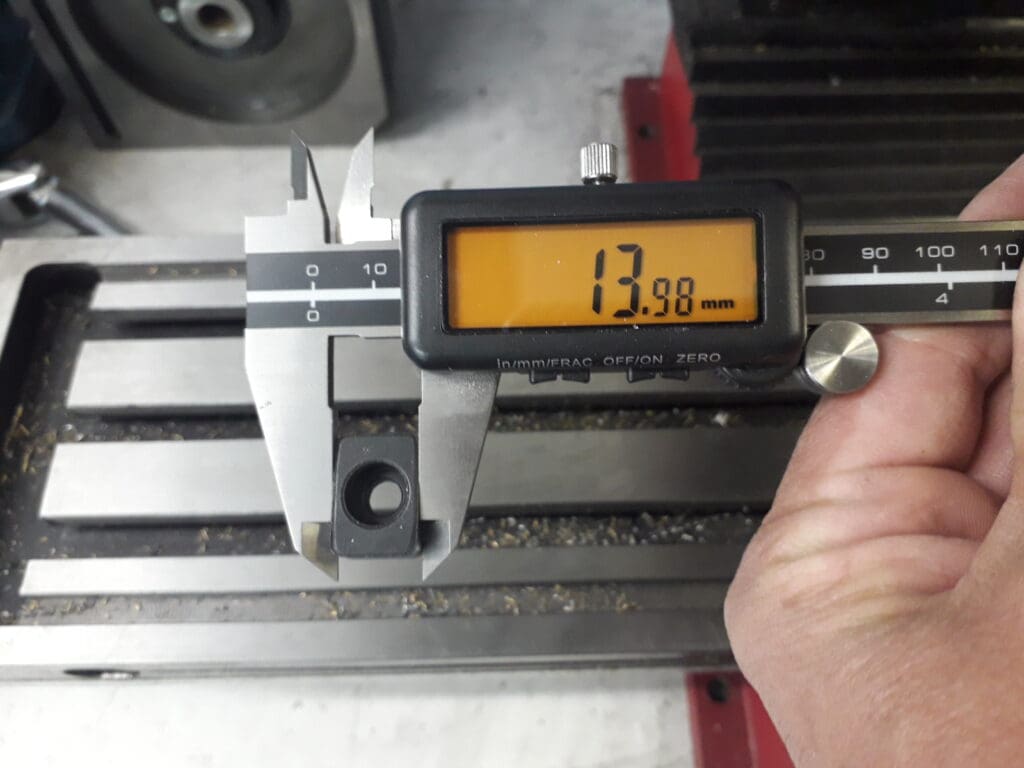
The fitting process starts by clamping a reasonably sized and straight square or rectangular bar to the mill table and clocking it as true a possible along the X-Axis. Photo 3 shows a 25mm square bar being positioned using a lever type Dti fixed to the underside of the head by it’s magnetic base.
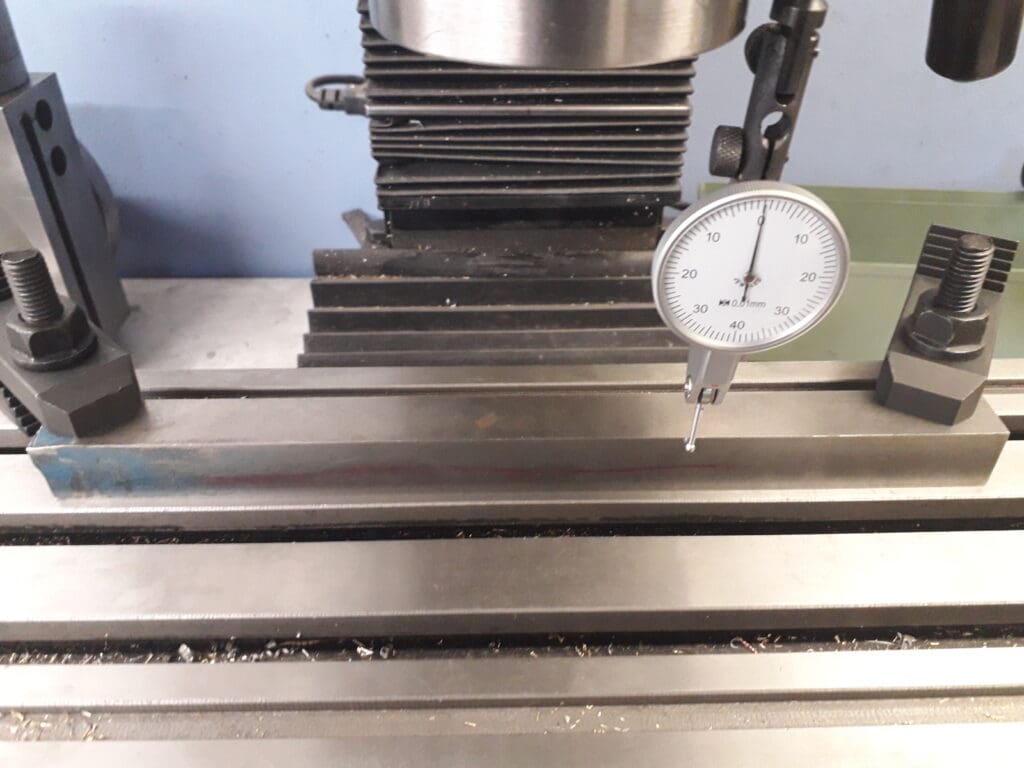
Having made sure that the vice is clean from swarf, particularly behind the fixed jaw if you have removed it at some time the vice can now be placed upside down over the bar and the jaws firmly tightened. Use an edge finder on either slide of the slot to find it’s centre and zero the Y-Axis hand wheel or DRO if you have one. Mark the keys and the vice so that they can go back into the same positions if you have the need to remove them at some time. I used single and double punch marks on the end of the keys and matching marks on the recessed underside of the vice. Photo 4.
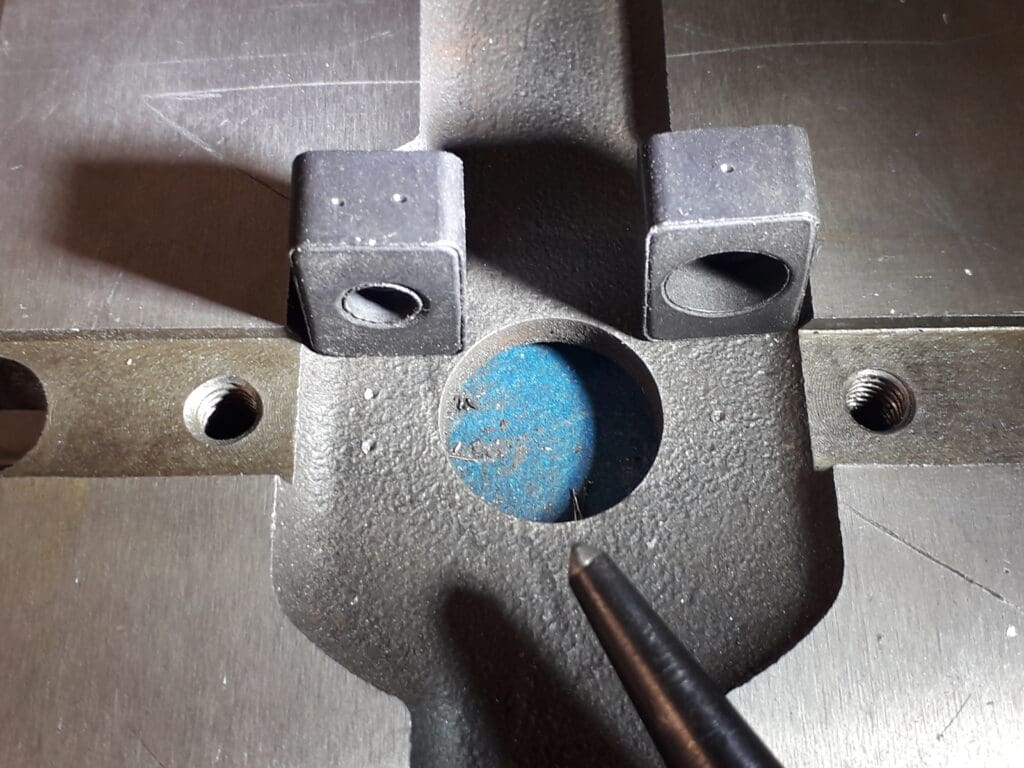
Before screwing the keys to the underside of the vice add a washer so that the key sit’s a bit proud of it’s final position, this will enable the sides to be machined without risking nicking the bottom face of the vice with your milling cutter. Photo 5. With the keys now firmly screwed in place on the washers bring the a milling cutter down to just above the vice, in photo 6 I am using a 0.1mm feeler gauge to ensure the cutter is clear.
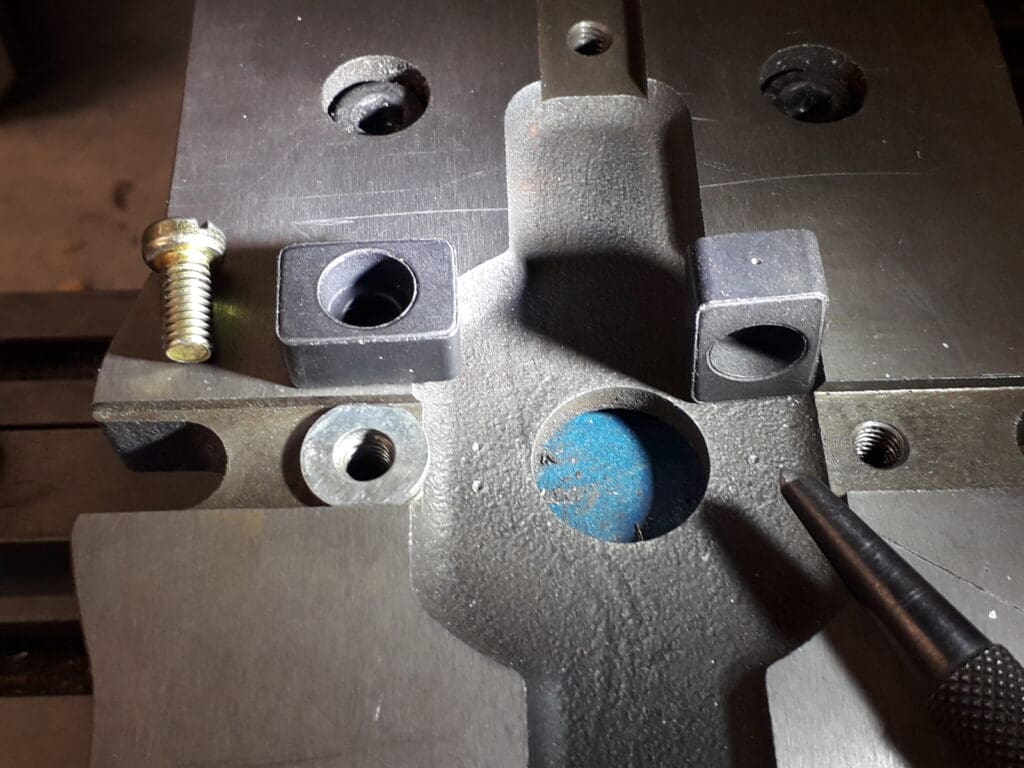
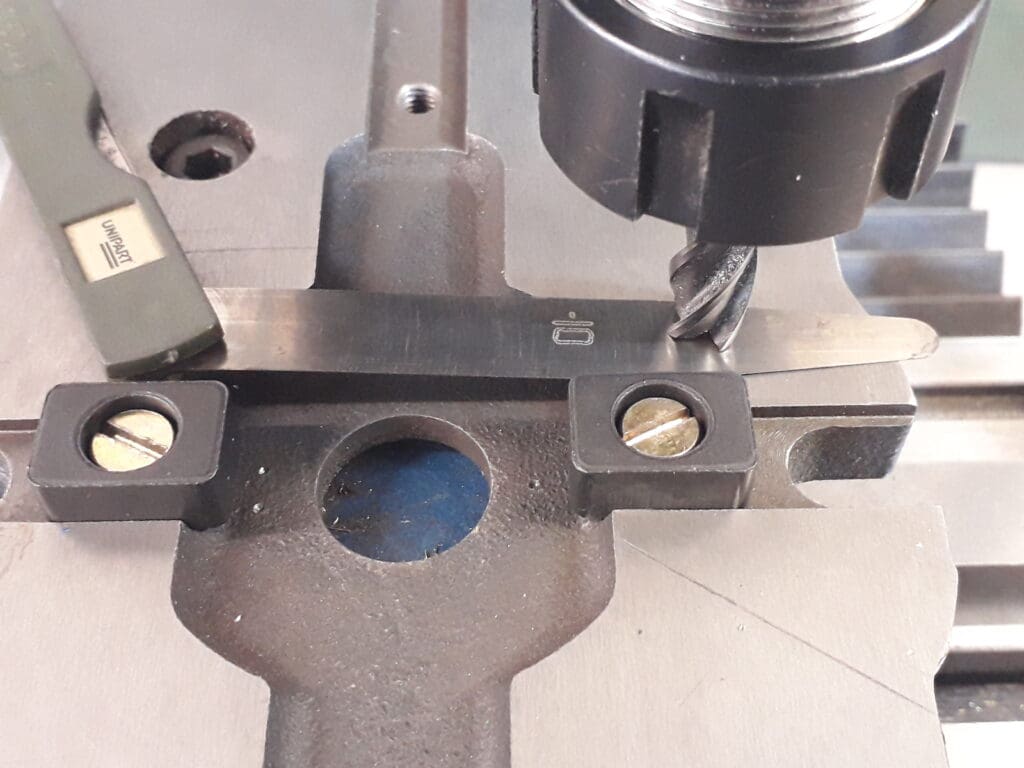
It is now just a case of taking equal amounts off either side of the keys until they are just below the width of the tee slot that was measured earlier, something like 0.05 to 0.1mm undersize will do which is 11.90mm to 11.95mm for a 12mm tee slot. Photo 7.
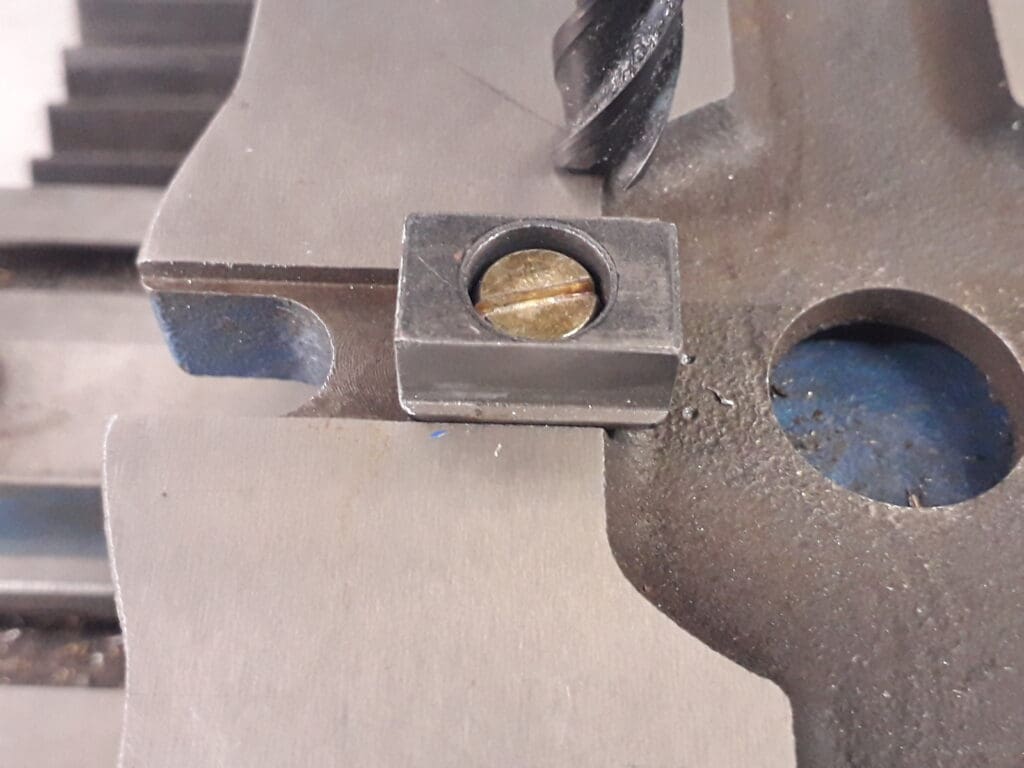
Remove the keys and with a fine file remove any burrs then reassemble into the slot but this time without the spacing washers and that is the job done. In use the vice is put into position and gently pushed back so the keys rest against the far edge of the keyway while the clamping screws or nuts are tightened. With luck you should have a vice that can quickly be positioned with an accuracy of 0.01mm over it’s jaw length which equated to approx 0.007degrees which is good enough for most jobs. If there is something special than needs more accuracy it should not take long to clock the vice in as you will be starting not far from where you want to be. The video shows the results from just pushing the vice with its machined in-situ keys back against the central tee slot.
No slot or keys?
If your vice is not equipped with the locating slot then mount it upside down as has been shown and locate the middle of the hold down lugs and use that as the Y position to mill a slot say 12mm wide and 2mm deep. Use a 10mm dia tool doing a central pass first then open up equally on each side using the material you will make the keys from to gauge the final width. Tap the hole M4. The keys can be 12mm wide x 10mm high and around 16-20mm long, drilled M4 clearance and counter bored to clear the head of an M4 cap head screw.
