We had some comments that the archive article in MEW 344 was rather difficult to read.
Many thanks to reader David Frith for re-scanning the article in question and putting it through OCR. Here’s the text:
Allan Jeeves discloses the secrets of the Griptru chuck.
Enjoy more Model Engineer reading in the monthly magazine.
Click here to subscribe & save.
Self centring 3-jaw chucks are an innovation of the 19th century and were a successful method of speeding up the chucking of work In the lathe. The 4•jaw independent chuck, which was a natural progression from the era of faceplate dogs which could be separately adjusted to centre the work (or throw it off-centre as the case may be), was a means by which a job could be exceptionally accurately centred, but precious time was spent in so doing . If it is not essential for the workpiece to be running deed true, for example if all the turning operations are to be carried out in one single chucking, the self centring chuck is ideal. Contrary to the belief held by many engineers, these chucks are not intended to operate ‘dead true’. Although work Is sometimes set up quite accurately by this method of workholding, any such exactitude is unanticipated and concentric accuracy of 0.076mm (0.003in.) at 25mm overhang is considered good while 0.127mm (0.005in.) Is often the case. especially if any wear has taken place.
If these chucks were Intended to provide the benefit of exact concentricity, chucks such as the 3-jaw combination chuck Introduced by Pratts of Halifax. West Yorkshire, a particular type of 3-jaw chuck where the jaws can be accurately adjusted individually prior to being manipulated simultaneously in the usual way – would not have been developed. You can walk Into almost any engineering jobbing shop and see 3-law chucks which have a ‘fairy circle’ of punch dots around one of the 3 pinion square drives where the chuck key is located. Presumably by using only this pinion to tighten the chuck, greater accuracy is possible than would be the case if the scroll is rotated by one of the other two pinions.
The year 1954 saw the introduction – by chuck manufacturers F. Burnerd & Co. Ltd. then of Kidbrooke, London – (now incorporated within Pratt Burnerd International of Halifax) of a micro adjustable 3-jaw, geared scroll chuck having the facility of adjusting the concentric location of the chuck unit relative to its mounting on the lathe spindle. That is to say that when the chuck has been secured to the spindle nose of the machine, it can then be accurately adjusted so as to become precisely concentric with the spindle, This feature bestows the chuck with the provision to be set up to within 0.005mm (0.0002in.) needle movement on the dial indicator, correcting the accumulated error of the individual parts when assembled, or compensating for any inaccuracy which may have occurred through reasonable wear and tear of the chuck. This product was named the Griptru chuck. Even in 1954 the concept of moving the chuck slightly once it had boon mounted was nothing new. In its simplest form the back plate or adaptor plate which Is normally located to the chuck body by a precise fitting spigot register is. instead. provided with a small clearance which allows the body to be tapped true before the securing screws have been finally tightened (fig.1). The most conspicuous disadvantage with this method is, of course, in the fact that the body can move on the spigot when in use due to the forces present during its operation.
The Griptru chuck is, however, something different. Once set up and secured In position, there Is no possibility of the chuck body moving on the spigot register and the device remains an accurate unit throughout its use. The principle of this chuck is fundamentally the same as that shown in fig.1 except that the body Is not tapped true with a mallet but is adjusted by means of 3 conical wedge screws which have hexagonal socket heads and so are moved using an Allen key. The chucks are originally supplied with the appropriate hexagon key machined onto one end of the chuck key tommy bar, an additional feature of this product.
The register spigot is machined with 3 tangential circular grooves which are milled in, equi-spaced, and form the bearing surfaces for the screw wedges (fig.2). These in turn are located In holes which are drilled tangentially in the body. The screws have conical shanks so that when they are screwed Inwards they displace the body in relation to the adaptor plate. This is done with the tension on the securing screws relaxed. The movement of the chuck body is so slight when the conical screws are turned that the adjustment is very fine and perfectly within the control of the operator. Once he is satisfied with the truth of the chuck the securing screws are finally tightened.
These chucks were first supplied in 3 1/2, 4, 5 and 6in. diameters; larger sires were introduced later, notably 8, 10 1/2. and 12 inches. They are now supplied in metric sizes and 6 jaw models are also available. A 4in. (100mm) diameter Griptru chuck has also been produced for direct mounting onto a Myford ML7 or Super 7 lathe.
While these chucks are quite expensive to purchase new, due to the fact that they have been on the market for 40 years or so secondhand examples are commonly found and don’t seem to command a higher price than a standard 3-jaw of the same diameter and condition.
I hope that this short article will assist the home workshop enthusiast In recognising this excellent work holding device if he is fortunate enough to encounter one at a bargain price.
Caption
The component parts of a 6in. Griptru chuck. They are identical to a standard 3 jaw chuck with the exception of the three conical wedge screws below the geared spiral ring on the left of the picture.
And here’s the scan, unfortunately as a jpg as I can’t seem to upload the original png; it’s better than the one printed in MEW but still a little blurred:
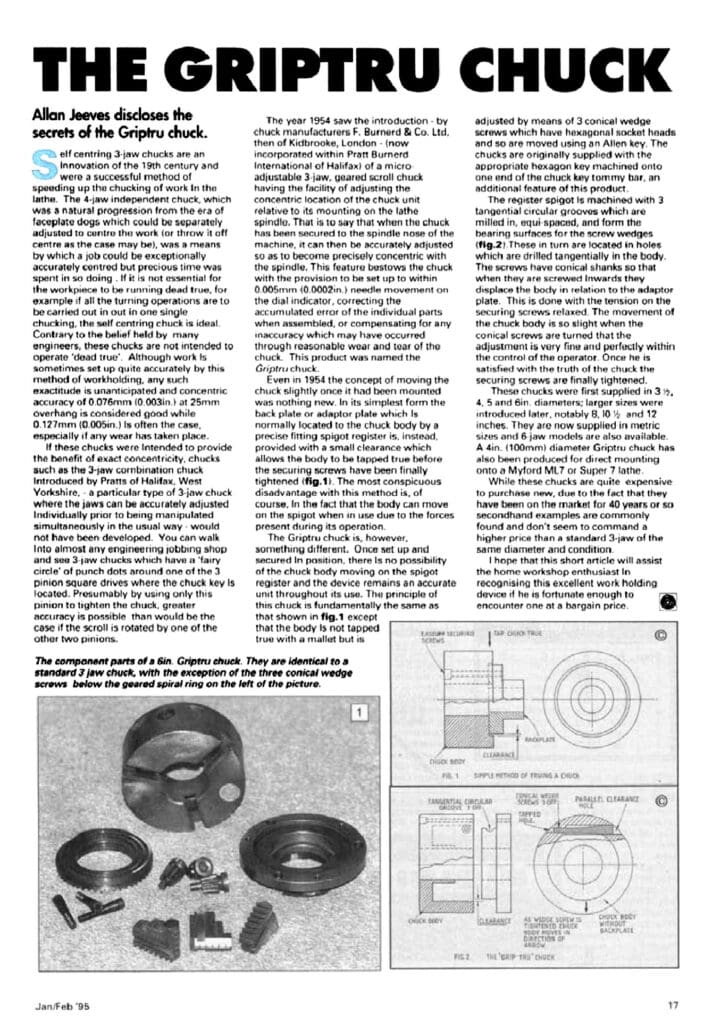